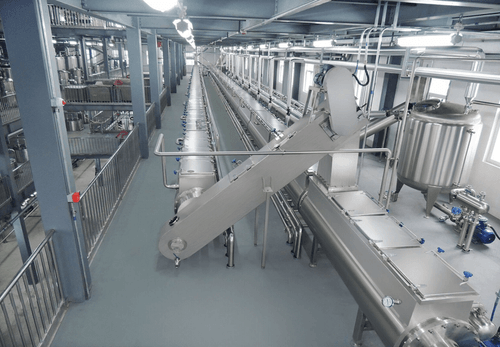
Continuous Extraction Unit
1、Traditional extraction tanks
Extraction tank is the most commonly used equipment for plant extraction. Herb and solvent are put into the tank and heated by hot water or steam in external jacket of the tank.The liquid extract is discharged through a sieve at the bottom of the tank. Fresh solvent is added into the tank for secondary extraction or triple extraction.
In small-scale production, the extraction tank is competent.
With the expansion of the production scale and the intensification of the industry competition, the defects of the traditional technology gradually appear , such as: low efficiency, large amount of labor, insufficient extraction, high energy consumption, low degree of automation, quality fluctuations ,etc.
With the expansion of extraction scale, increasing quantity and volume of extraction tanks shall not be the best solution.
2、Continuous extraction units
The extraction tank is designed as a horizontal channel , and a push device is installed inside.
Herb material and fresh solvent are fed into the channel quantitatively and moves continuously through the channel. Both are heated by the heat medium in the outer jacket during the process.The whole process is kept on the process temperature required for extraction.
Fresh solvent is preheated and herb material is prewetted before entering the channel .
The extraction tank is divided into several stages: stage A-stage B , or , stage A-stage B-stage C.
Herb material running from stage A to stage C, while fresh solvent running from stage C to stage A. As the herb material and the solvent running in reverse direction, the soluble ingredients of solid phase (herb material) can be fully released, and solvent consumption can be minimized.
When necessary, screw extruders can be installed between two extraction stages for a complete extraction.
Detailed Introduction:
A. High efficiency
Continuous and flow-line production, capability of single unit vary from. 100 kg/h to 2000 kg/h(dry material).
B. Lower running cost
Reducing liquid-solid ratio from 12-20 to 5-9,total amount of the extract liquid is reduced ——that means greatly reduce energy consumption of subsequent evaporation equipment and equipment specification.
Human labor is reduced. Only 2~3 workers needed.
C. Higher yield
The extraction yield was 10 ~ 15% higher than that of extraction tanks.
D. Stable quality
As the unit is running continuously, and temperature is kept in the same level in each extraction stage. Stability and consistency of the unit is much better than extraction tanks.
E. Wide Adaptability
Thanks to the design of the push device, the system can be applied to a variety of plant or animal
materials.
The unit is explosion-proof, various solvent such as water ,alcohol ,methanol, ethyl acetate can be used.
F. Lower investment on infrastructure
The unit is installed directly on ground.
Workshop needed is only 5 meters high.
The unit can be installed in different layers or in the same layer according to requirements.
4、Main Composition of the Unit
- Raw material prewetting module
- Solvent preheating and dosing module
- Continuous extraction mainframe
- Residue drying module
- Extract fluid filtering module
- Circulating water module
- Control module
5、Equipment selection
Please tell us the basic parameters as below:
A. Product name and extracting capacity (kg/h).
B. Material size of and natural density of dry material.
C. Past extraction process(approximate) .
D. Solvent and temperature requirement.
Please see the Inquiry. We will make quotation according to the Inquiry.
Device In Workshop:
Company Profile
We was founded in 2002, We are a high-tech enterprise in Zhejiang province. We specilize in the design, production and installation of phermaceutical machnery, chemical machinery, dairy & food machinery, sanitary fuid equipment and intelligent control system for Traditional Chinese medicine (TOM). We are the member of "China Association for Pharmaceutical equipment".
Company main products and services:
extractor and concentrator equipments, vacuum belt drying equipmenst, purifying and distillation equipment, chemiacal equipments and other non-standard equipments, pumps, fluid pipe fittings and also can provide users with automatic control DCS, Warehouse Management System WMS, manufacturing execution system MES overall planning and design, euipment installation and commissioning services, and undertake turnkey projects.
Office and Manufacturing Workshop
Company personnel: there are more than 200 employees (1 Professor, 5 senior engineers, 16 engineers, 46 technicians, 2 senior technicians, 1 technician and 12 senior workers)
Customer Case